Having worked as a simulation engineer for many years now, I have done my fair share of meshing with hexahedral (hex) and tet (tetrahedral) elements.
To help you understand the differences between the two, I’ll explain what each type of mesh is, and when it’s best to use one type over another.
As a general rule, hexahedral (hex) meshes are more accurate than tetrahedral (tet) meshes while requiring less computing power and shorter solve times. That said, tetrahedral (tet) elements are a good option for complex geometry when creating a hexahedral (hex) mesh is time-consuming.
At one time, hexahedral (hex) elements were the chosen option for many experienced simulation engineers because of the higher level of accuracy.
However, with modern solvers and experience, I have learned that the extra accuracy supplied by hexahedral elements is offset by the fast meshing speeds that are capable with tetrahedral (tet) meshes.
At the end of the day, it is about understanding the physics of your problem and ensuring that your mesh has captured the intent of the simulation.
In this article, I will discuss hex versus tet meshes in more detail, covering:
- What is a hex mesh?
- What is a tet mesh?
- Is a hex mesh better than a tet mesh?
- What are the advantages of hex dominant mesh?
- What are the advantages of tet dominant mesh?
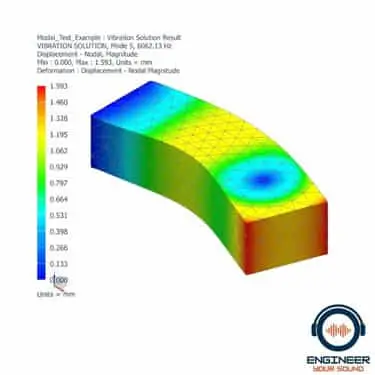
What Is A Hex Mesh?
A hexahedral mesh (hex mesh) is composed of six-sided elements that form a three-dimensional grid or lattice structure. They are easy to construct and have excellent accuracy.
Here is an image of a cylinder meshed using hexahedral elements. You can see the brick and “square-like” element shape.
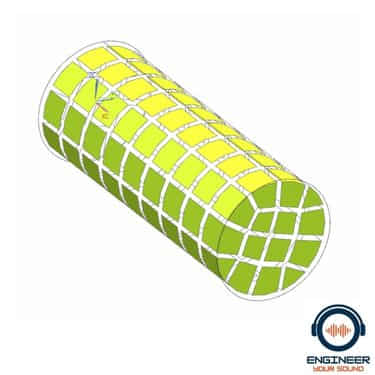
We often use Hex meshes as a benchmark when developing new algorithms and techniques for structural analysis, because of their excellent geometric properties. However, they can be difficult to construct in highly curved geometries because of the large number of elements required.
Imagine you have a geometry with complex and curved surfaces. Trying to sub-divide the CAD geometry to create a hexahedral mesh can be done (I have completed a lot of this in my career), however, this is time-consuming and will require a lot of simulation skills to do quickly.
For more complex geometry, the better trade-off of your time could be to use a tetrahedral mesh.
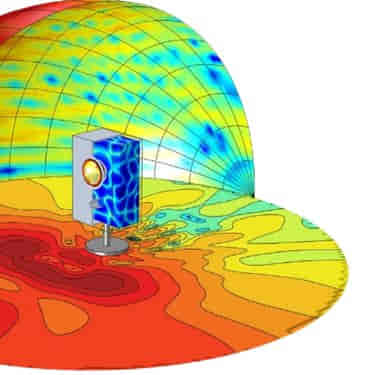
Learn Finite Element Analysis Get An Industry Qualification!
What Is A Tet Mesh?
Tetrahedral meshes (tet mesh) comprise four-sided pyramids that form a three-dimensional structure. They are suitable for highly curved and complex geometries because of their flexibility and ease of implementation.
Here is an image of a cylinder meshed using tet elements. In reality, you would use hex elements for this simple geometry, but you can see the pyramid-shaped elements in this image.
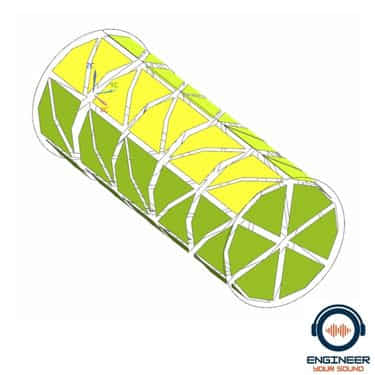
Tet meshes have slightly less accuracy than hex meshes, but with the right techniques, they can still provide accurate results.
The idea that hexahedral meshes are the only way forward for serious and professional simulation engineers is simply outdated in my opinion.
For the right geometry, a tet mesh can be a good and fast way to mesh complex geometry.
Is A Hex Mesh Better Than A Tet Mesh?
It depends on the situation. Each type of mesh has its own strengths and weaknesses, and which one is better can depend on the application or usage.
For most applications, a hexahedral (hex) mesh will provide better accuracy than a tetrahedral (tet) mesh because of its improved cell quality and stability. However, for curved surfaces where you need more flexibility, a tet mesh may be more suitable.
Ultimately, it is best to assess the specific needs of each individual project when making this decision.
Many studies have been done in recent times which have compared the benefits of hex and tet meshes. For example, this is an excellent study which compares both element types, concluding that quadratic tetrahedral elements are a valid option compared to hexahedral elements for their application. [source]
For professional simulation engineers, time is crucial, and it is possible to spend hours meshing complex geometry if you are forced to use a hex mesh.
In recent years, I have used a tetrahedral mesh for complex geometry. With the physics problems I work on daily, which are acoustic, I can quickly mesh a complex geometry using a tet mesh and solve it without too much loss of accuracy.
Of course, solve times with tetrahedral meshes are a lot longer and can take more processing power. However, if you have the bandwidth a slower and processor-heavy solve might be an okay compromise for you.
If you are concerned or not convinced that you have chosen the right element type, it is best to complete an experiment.
Mesh your geometry with hexahedral and tetrahedral elements, check for convergence and then compare the results.
At the end of the day, your ultimate goal is reliable and verifiable simulation results. As long as you meet this goal, you can be confident that you have picked the right element type.
What Are The Advantages Of Hex Dominant Mesh?
Hexahedral meshes, or ‘hex meshes’, offer several advantages over tetrahedral meshes.
1. Greater Accuracy
One of the major advantages of a hex mesh is that they allow for more accurate simulations due to its higher resolution and more consistent element size. Hexahedral elements are also better at preserving internal angles, which helps maintain the accuracy of the simulation results.
2. Less Computing Power
Hexahedral meshes require less computing power than tetrahedral meshes, thanks to their simplified shapes.
3. Faster Solve Times
Hexahedral meshes result in faster run times when compared with tetrahedrons, which makes them ideal for large-scale problems.
4. Versatile
We can easily adapt hexahedral elements to fit curved boundaries, making them suitable for a wide range of geometries.
What Are The Advantages Of Tet Dominant Mesh?
In my view, the primary advantage of tetrahedral meshes, or ‘tet meshes’, is that they provide a quick way to mesh complex geometry.
In addition, I have found that tetrahedral meshes offer greater flexibility when adapting to new geometries.
For example, if an analysis requires the mesh to be changed during the simulation run time—such as adding or deleting elements or even modifying the CAD geometry—tetrahedrons can easily accommodate this change without having to completely redo the mesh.
Overall, while both hexahedral and tetrahedral meshes have advantages and drawbacks depending on the application, tetrahedrons tend to be more suitable for simulations involving complex geometry because of their improved ability to accurately represent curved surfaces.
Final Thoughts
In conclusion, it is important to consider the advantages and disadvantages of each type of mesh when selecting one for your finite element analysis.
Hexahedral meshes are more accurate due to their higher resolution and require less computing power than tetrahedrons. However, they can be difficult to adapt in complex geometries compared to tetrahedral meshes which have greater flexibility.
Ultimately, depending on the application you’re using them for, both hex dominant or tet dominant meshes offer unique benefits that you should not overlook when choosing a solution.
It is important to assess the needs of each project before deciding on which type of mesh works best
To decide which type of mesh is best for your project, consider the geometry of the object being simulated. If the geometry is relatively simple and can be easily subdivided, then the hex mesh is a good choice because of its high accuracy and simple geometric properties.
On the other hand, if the object has complex curvatures or intricate details, then the tet mesh may be your best option due to its flexibility, speed and ease of implementation.
Overall, both types of meshes have their own unique advantages and disadvantages. When it comes to finite element analysis, the key is to choose the type of mesh that best fits your project’s needs. With careful selection, you can be sure to get accurate results no matter which type of mesh you choose.
To learn more about finite element analysis and get a qualification in the subject, I recommend Coursera as a wonderful educational resource.
Happy simulating!
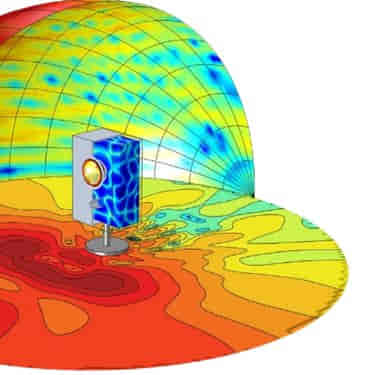