In the fascinating world of Finite Element Analysis (FEA), understanding the concept of boundary conditions is crucial.
Boundary conditions in FEA analysis define how a structure interacts with its surroundings. They include fixed supports, applied loads, displacements, and constraints. Boundary conditions ensure realistic simulation by simulating real-world conditions and capturing the behaviour of the structure accurately.
Whether it’s specifying a fixed support to mimic a clamp or applying a pressure load to simulate real-world conditions, these boundary conditions serve as grounding principles for our models.
In this article, I will delve deeper into the various types of boundary conditions, explaining how to choose the appropriate ones and their significance. Drawing from my personal experiences, I will share the reasons why I believe that boundary conditions are the most important aspect of an FEA simulation.
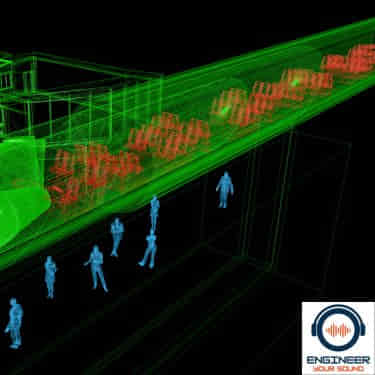
What Are Boundary Conditions In An FEA Analysis?
Boundary conditions in Finite Element Analysis (FEA) are essentially the set of constraints or conditions that you impose on your model for the simulation. These conditions provide detailed instructions on how the model should interact with its surrounding environment during the analysis.
Each type of boundary condition can significantly influence the outcome of the simulation, guiding how the model behaves under certain conditions.
Examples include specifying if a particular point is fixed or free to move or if a certain force is applied to a specific part of the structure.
Selecting the appropriate boundary conditions is a crucial step in the FEA process, as it ensures the accuracy and reliability of the simulation results.
What Is An Example Of A Boundary Condition?
An excellent example of a boundary condition in FEA is the application of a fixed support. Fixed supports, being one of the simplest types of boundary conditions, are commonly used in structural analysis. They involve constraining certain nodes or parts of a structure to remain static while the analysis is taking place.
Let’s imagine you’re analyzing a bridge; the ends of the bridge where it connects to the ground could be considered fixed supports. This means that those points are restrained from moving in any direction, simulating the bridge’s behaviour in real life.
By imposing this boundary condition, we can accurately predict how the bridge will react under various stresses and strains.
How Do I Know What Boundary Conditions To Apply?
Determining the appropriate boundary conditions to apply in an FEA analysis largely depends on the physical scenario being simulated. You must consider the nature of the structure, how it interacts with its environment, and what you’re trying to achieve with the simulation.
Start with a clear understanding of the physical problem, including any constraints or loads that may exist. For example, if you’re analyzing a car suspension system, the constraints might be where the suspension connects to the car body and wheel.
Forces could include the car’s weight and any additional loads it might carry.
In cases of uncertainty, it can be helpful to run multiple simulations with different boundary conditions to understand their impact on your results.
Personally, I always recommend discussing boundary conditions with your colleagues if you have any. If your boundary conditions do not stand up to peer scrutiny, then your simulation is questionable.
Remember, the accuracy of your simulation is heavily dependent on the boundary conditions applied, making their selection a crucial step in the FEA process.
Why Are Boundary Conditions Important?
Boundary conditions are indispensable in Finite Element Analysis, primarily because they allow for a more accurate and realistic representation of the physical world within the simulation. By defining how a structure interacts with its surroundings, such as the forces exerted on it, or the constraints it operates under, boundary conditions help to mimic real-world scenarios.
Consequently, this enhances the reliability of the simulation, making the findings more credible and applicable.
Furthermore, boundary conditions can significantly influence the outcome of the simulation, effectively making or breaking the model’s accuracy. For instance, an incorrect or inappropriate boundary condition might lead to incorrect stress or strain distributions, which in turn could lead to flawed design decisions.
In essence, the careful selection and application of boundary conditions are vital for the success of any FEA simulation.
How Do Boundary Conditions And Symmetry Work?
Symmetry in FEA offers a powerful tool for reducing problem size and computational time. By exploiting the symmetrical properties of a model, we can analyze a fraction of the model instead of the entire structure.
However, the correct application of symmetry boundary conditions is essential to ensure accurate results.
In a symmetric model, the boundary conditions ensure that the model behaves as if it were a part of the whole. They restrain displacements perpendicular to the plane of symmetry while enabling free movement along the plane.
For instance, in a bridge scenario, if we are modelling only half the bridge due to symmetry, we need to ensure that the nodes along the symmetry line are constrained in the direction perpendicular to the line. This ensures that the model behaves as though it’s still connected to the unmodelled half, preserving the integrity of the simulation.
Thus, boundary conditions and symmetry work hand in hand in FEA, driving efficiency without compromising on accuracy.
Examples Of Types Of Boundary Conditions
1. Fixed Support Boundary Condition
This is one of the simplest and most commonly used types of boundary conditions. In a fixed support condition, certain nodes or parts of the structure are constrained to remain static during the simulation. This is typically used when analyzing structures like bridges where the ends of the bridge (connecting it to the ground) are considered fixed supports.
2. Pinned or Hinge Support Boundary Condition
A pinned support or hinge support boundary condition allows rotation but does not allow translation along any axis. This type of boundary condition is commonly applied in scenarios where certain components are connected via a hinged connection, such as in truss structures.
3. Roller Support Boundary Condition
Roller supports are free to move in one direction, typically the direction along the surface on which they are resting. These types of supports are common in structures like conveyor belts or any structure that includes components designed to move along a certain path under load.
4. Free Boundary Condition
A free boundary condition is where no restraints are applied to the nodes of a structure or component. This condition is generally applied to nodes that do not interact with other components or support structures.
5. Force Boundary Condition
In this type of boundary condition, certain forces or loads are applied to specific nodes or areas of the structure. The precise nature of these forces can vary significantly based on the specifics of the simulation, including factors like the type and distribution of the load, its duration, and its direction.
6. Displacement Boundary Condition
Displacement boundary conditions specify a certain displacement value for a particular node or set of nodes. This displacement can either be a specific movement along certain axes or a rotation about certain axes.
Each of these boundary conditions can significantly influence the outcome of an FEA analysis and bring us closer to understanding the real-world behaviour of the structures we are analyzing. The choice of the right boundary condition often depends on the specifics of the model and the behaviour we are trying to simulate.
Loads Versus Constraints
When we talk about boundary conditions in FEA, we are not just talking about how a model is constrained. Loads applied to the model are also classified as boundary conditions.
In reality, boundary conditions must represent everything about the system that you have not modelled, for example, how a part is constrained and what loads are applied to it.
Below is a list of examples of the types of loads that can be applied to a simulation.
Types Of Loads In FEA Simulation
- Point Load: This load is applied at a single point of the structure. It’s common in structures like bridge supports, where the load is concentrated on specific points.
- Distributed Load: This load is spread across a surface or line. It’s often used when modelling weight distribution in structures like beams and floors.
- Moment Load: This load tries to rotate the object around a point or line. It’s crucial for simulating structures subjected to torsion, like shafts and axles.
- Temperature Load: This factor is in the expansion or contraction of materials due to temperature changes. It’s important in simulations dealing with thermal stresses.
- Pressure Load: This load is applied over an area, typically over the entire surface of the object, like in hydraulic or pneumatic systems.
- Gravity Load: This accounts for the force of gravity acting downward on all elements of the model. It’s important in virtually all structural simulations.
Understanding and correctly applying these loads in simulations is crucial in accurately predicting real-world behaviour and, in turn, designing more effective, safe, and efficient structures.
Types of Constraints in FEA Simulation
Below is a list of examples of the types of constraints that can be applied to a simulation.
- Fixed Constraint: This type of constraint prevents any form of movement or rotation. It’s equivalent to securing the object in place.
- Displacement Constraint: This puts a limit on the movement of the object in one or more directions. The displacement can be zero (a common scenario) or a specific value.
- Rotation Constraint: This restricts the rotation of the object about one or more axes. Like displacement constraint, the rotation can either be zero or a specific value.
- Frictional Constraint: This simulates the resistance to motion due to friction when an object is in contact with another. It plays a significant role in simulations involving gears, wheels, or any moving parts in contact.
- Symmetry Constraint: This confines the movement of the object based on the symmetry of the model. It’s crucial for efficient computation in symmetric models, as discussed earlier.
- Periodic Constraint: This constraint ensures the same boundary condition for two or more points in the model. It’s commonly used in repeating structures like heat sinks and building floors.
The correct application of these constraints is key to creating a successful simulation, and they must be chosen carefully to represent real-world conditions accurately.
Final Thoughts
The application of appropriate boundary conditions in Finite Element Analysis (FEA) is a fundamental aspect of achieving reliable and accurate results.
Understanding the different types of loads and constraints, along with the conditions under which they are applied, can greatly enhance the precision of your simulations.
It’s important to remember that while FEA is an incredibly powerful tool, its accuracy is heavily dependent on the user’s understanding and correct application of these conditions.
Always ensure to account for all the real-world conditions that your model may be subjected to for an effective, safe, and efficient design.