In finite element analysis (FEA), understanding the nuanced differences between linear and nonlinear analysis is crucial. While both approaches provide valuable insights, the circumstances under which you select each can significantly impact your results.
Linear finite element analysis assumes the relationship between loading and response is linear, while nonlinear finite element analysis considers material and geometric nonlinearities.
Linear analysis is suitable for small deformations and linearly elastic materials, while nonlinear analysis captures large deformations, nonlinear material behaviour, and contact interactions.
In this article, I will explain linear and nonlinear analysis, highlighting their distinct characteristics and appropriate usage scenarios and sharing my experiences working with both linear and nonlinear analysis as a simulation application engineer.
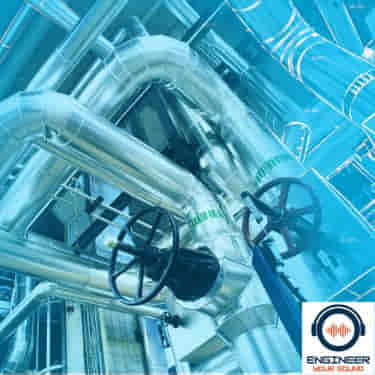
What Is A Linear Analysis?
In simplest terms, a linear analysis is a type of finite element analysis where the relationship between the applied forces and displacements is assumed to be linear. This means the material’s deformation is directly proportional to the forces applied, aligning with Hooke’s Law.
Linear analysis is typically used when dealing with small deformations and linearly elastic materials, which return to their original shape after the forces are removed. This type of analysis can be utilized effectively for problems with a relatively small scale of deformation where the structure’s stiffness remains constant throughout.
It’s a less computationally intensive analysis, providing faster results, which makes it ideal for preliminary design evaluations.
What Is A Nonlinear Analysis?
A nonlinear analysis, in contrast, is a type of finite element analysis that takes into account the nonlinearities in the material properties, geometry, and boundary conditions. This means that the output response does not have a simple, direct proportionality to the input loads.
Nonlinear analysis is often necessary when dealing with large deformations, nonlinear material behaviour (like plasticity, hyperelasticity, or creep), and complex contact interactions.
Unlike in linear analysis, the structure’s stiffness in a nonlinear analysis may vary during deformation, requiring repeated stiffness updates and equilibrium iterations within a single load step, thus making it more computationally demanding.
However, nonlinear analysis is capable of providing more accurate and realistic results for complex real-world problems where linear assumptions do not hold.
What Is The Difference Between Linear And Nonlinear Analysis?
The primary difference between linear and nonlinear analysis lies in the assumptions made about the relationship between applied forces and the resulting displacements. In a linear analysis, this relationship is assumed to be proportional and linear, abiding by Hooke’s Law. This type of analysis is appropriate when dealing with small deformations, linearly elastic materials, and situations where the stiffness of the structure remains unchanged.
In contrast, nonlinear analysis does not assume a simple proportional relationship. It accounts for nonlinear material behaviour, large deformations, and complex contact interactions. Changes in the stiffness of the structure due to deformation are also taken into account, requiring iterative processes for each load step. This makes it much more computationally intensive than a linear analysis, but it provides more accurate and realistic results for complex scenarios where the assumptions of linear analysis do not hold.
Another critical difference is the application. While linear analysis is excellent for preliminary design evaluations due to its less demanding computational needs, nonlinear analysis is essential when a more accurate representation of real-world scenarios is required, especially when dealing with large deformations and nonlinear materials.
It’s important to note that the choice between linear and nonlinear analysis is dictated by the problem at hand, the resources available, and the accuracy required in the results.
Pros And Cons Of Linear Analysis
Pros Of Linear Analysis
- Computational Efficiency: As mentioned previously, linear analysis is less computationally intensive than nonlinear analysis. This means that it can provide results faster, making it ideal for preliminary design evaluations or when dealing with a tight project timeline.
- Simplicity: Linear analysis is also simpler to implement and interpret. It operates on the direct proportionality between applied forces and deformations (Hooke’s Law), which is easier to understand and model.
- Suitability for Small Deformations: For problems where deformations are small and material remains within its elastic limit, the linear analysis provides a reliable and accurate solution.
Cons Of Linear Analysis
- Limited Scope: The main drawback of linear analysis is that it can only account for linearly elastic materials and small deformations. It cannot accurately predict behaviour for large deformations or for materials showing plasticity, creep, or hyperelasticity.
- Inaccuracy in Complex Scenarios: In situations where the structure’s stiffness changes due to deformation or where complex contact interactions occur, linear analysis may lead to inaccuracies as it does not consider these nonlinearities.
- Lack of Real-World Representation: In many real-world situations, material behaviour and structural response are not linear. Therefore, relying on linear analysis in these cases can result in unrealistic or misleading results.
Overall, while linear analysis has its place in the toolkit of finite element analysis, it’s crucial to understand its limitations and apply it appropriately.
Pros And Cons Of Nonlinear Analysis
Pros Of Nonlinear Analysis
- Versatility: Nonlinear analysis can handle a wider range of problems than linear analysis. It can accurately model and predict behaviour under large deformations, complex contact interactions, and nonlinear material behaviour, including plasticity, hyperelasticity, and creep.
- More Accurate Real-World Representation: By accounting for changes in the structure’s stiffness during deformation and complex contact interactions, nonlinear analysis can provide a more realistic representation of real-world scenarios.
- Suitability for Complex Scenarios: Nonlinear analysis is necessary when the problem involves situations where the assumptions of linear analysis do not hold. It can provide accurate and reliable results for complex scenarios.
Cons Of Nonlinear Analysis
- Computational Intensity: Nonlinear analysis is computationally more intensive than linear analysis. This is due to the need for repeated stiffness updates and equilibrium iterations within a single load step. Therefore, it takes a longer time to get results.
- Complexity: Implementing and interpreting nonlinear analysis can be more complex due to the nonlinearities involved. It requires a deeper understanding of the mechanics and the material behaviour.
- Resource Intensive: Due to its computational demands, nonlinear analysis requires more resources, such as computing power and time, making it potentially more expensive to use.
In summary, while nonlinear analysis can provide a more accurate representation of real-world scenarios, it comes with its own set of challenges and requirements. The choice between linear and nonlinear analysis should be made based on a careful consideration of the problem at hand, the available resources, and the level of accuracy required.
Examples Of A Linear Analysis
A classic example of a linear analysis is the design and analysis of a simple steel beam. Here, the material’s behaviour is linear (as steel behaves elastically until its yield stress), the deformations are small, and the structure’s stiffness remains constant. This makes it a perfect candidate for a linear analysis.
Another example is the stress analysis of a plate with a small hole under uniform tension. As long as the material remains elastic and the deformations are small, a linear analysis can accurately predict the stress concentration around the hole.
Lastly, a linear analysis is often used in the preliminary design stages of a building structure. Engineers can perform a linear static analysis to quickly assess the structural response under the expected loads, allowing them to make necessary design modifications before moving into more detailed and computationally intensive, nonlinear analyses.
Examples Of A Nonlinear Analysis
One common scenario where nonlinear analysis is employed is in the study of large deformation problems, such as a rubber band being stretched. As the rubber band stretches, its stiffness changes significantly, and the material shows clear nonlinear elasticity. A linear analysis would not be able to accurately predict the behaviour in this case.
Another example is the analysis of plastic deformation in metal-forming processes. Here, the material undergoes permanent deformation and behaves plastically. The stress-strain relationship is nonlinear and requires a nonlinear analysis to accurately predict the product’s final shape and the forces required for the process.
A third instance can be seen in the study of contact problems, such as the crash analysis of vehicles. This involves complex contact interactions and large deformations beyond the scope of linear analysis. Nonlinear analysis accurately captures the behaviour during such high-impact scenarios, thus providing critical insights for design and safety measures.
How Do You Tell If An Analysis Should Be Linear Or Nonlinear?
The decision to perform a linear or nonlinear analysis hinges on understanding the nature of the problem at hand. With a few key considerations, you can discern the appropriate analysis type.
Firstly, it’s essential to evaluate the material’s behaviour. If the material remains within its elastic limit and the resulting deformations are small, a linear analysis would be applicable. On the other hand, if the material exhibits plasticity, creep, or hyperelasticity, a nonlinear analysis would be necessary.
Secondly, consider the magnitude of the deformations. For small deformations where the structure’s stiffness remains constant, a linear analysis suffices. However, for large deformations, where the stiffness changes significantly, a nonlinear analysis is required.
Finally, examine the complexity of the contact interactions. If the scenario involves straightforward interactions, a linear analysis might suffice; however, in cases where complex contact interactions occur, a nonlinear analysis would provide a more accurate representation.
Remember, the goal is to choose the approach that provides a balance between computational efficiency and the accuracy necessary for your application. Always consider the physical phenomena you wish to capture and the resources available before deciding between a linear or nonlinear analysis.
Should I Complete A Linear Or Nonlinear Analysis?
Deciding whether to complete a linear or nonlinear analysis primarily depends on the nature of your problem and the required level of precision. If you’re dealing with a problem where material behaviour remains within its elastic limit, and deformations are small, a linear analysis can be an efficient and effective choice. It’s often suitable for preliminary design stages when you need results quickly to guide your design modifications.
However, if your problem involves significant deformations, complex contact interactions, or nonlinear material behaviours (like plasticity or hyperelasticity), then a nonlinear analysis is necessary to provide an accurate representation of real-world scenarios. Nevertheless, bear in mind that nonlinear analysis is computationally intensive and may require more time, expertise, and resources.
It’s all about balancing the need for accuracy with computational efficiency. Key factors to consider include the behaviour of the material, the size of deformations, and the complexity of contact interactions. Your decision should be grounded in a thorough understanding of the problem at hand, the resources you have available, and the accuracy required for your specific application.
Final Thoughts
The choice between linear and nonlinear analysis is a fundamental aspect of engineering and scientific challenges, with a significant influence on the accuracy of the outcomes and computational efficiency.
Understanding the material behaviour, deformation levels, and the complexity of contact interactions helps in making this crucial decision.
A linear analysis is best applied in scenarios with small deformations and where the material remains within its elastic limit. However, for large deformations, complex contact interactions, or nonlinear material behaviours, a nonlinear analysis is more suitable.
Remember, the key lies in striking a balance between computational efficiency and the necessary level of accuracy for your specific project or application.