Finite Element Analysis (FEA) and Finite Element Method (FEM) are two powerful tools used to analyse the behaviour of structures and systems under various loading conditions.
Working as a professional simulation engineer, I hear the term FEA and FEM being used interchangeably every day and therefore, it can be confusing for new engineers to understand these terms and what the difference is between FEA and FEM.
As a general rule, FEM refers to the general process of discretizing a continuous problem into smaller elements and solving them, while FEA refers to the numerical process of approximating solutions to these problems.
In other words, FEM is a set of rules that govern how engineering problems can be solved, whereas FEA is the actual method used to solve these problems.
In reality, which term you use depends on the context. I do not think anyone will be too concerned if you use the terms FEA and FEM interchangeably, as they are part of the same world.
For example, I could say “I need to use FEM to solve this problem” and then say, “I have completed FEA on this problem”.
In this article, I will dig deeper into these terms, sharing what I have learned from working as a professional simulation engineer for 15 years, covering:
- What is the difference between FEM and FEA?
- What is FEA used for?
- What are the advantages of FEM and FEA?
- What are the different types of FEM?
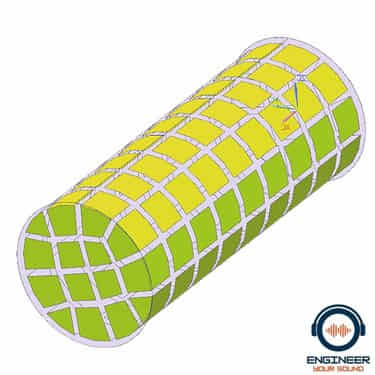
What Is The Difference Between FEM And FEA?
FEM stands for Finite Element Method, which is an analytical tool used in engineering and physics to analyse a wide range of phenomena. This method involves dividing a physical system into many small elements that are connected by nodes.
Each element is then solved using differential equations, numerical methods, and sometimes analytical techniques. The resulting solution provides a detailed understanding of the physical system, including its behaviour under different loading conditions.
FEA stands for Finite Element Analysis, which is the application of FEM to study and solve complex engineering problems.
There is no difference between FEM and FEA. One term refers to the method (Finite Element Method) used to describe a complex engineering problem, while the other refers to the application (Finite Element Analysis) of the method to real-world simulation problems.
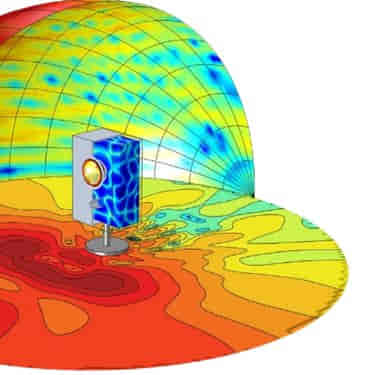
Learn Finite Element Analysis Get An Industry Qualification!
What Is FEA Used For?
FEA is widely used in various engineering fields as it provides a comprehensive method of analysing complex physical systems. It can be used to analyse stress and strain in structures, fluid dynamics, heat transfer, thermal stresses, and many more. FEA can also be used to predict how materials behave under different loading conditions, and to optimise the design of components.
FEA is particularly useful in the automotive and aerospace industries, where it can be used to study how structures respond under extreme loading conditions. It is also essential for predicting how structures will behave in a crash situation or during high-speed manoeuvres.
FEA (FEM) comes under the umbrella of predictive engineering. I use FEA in my engineering role to predict how a design will react to stress and vibrations in the real world.
We can simulate a design, apply material properties and inspect the results to ensure that the design will behave as we would like in the real world.
This can save a lot of time and money manufacturing failing prototypes and increase the probability of getting designs right the first time.
To learn about the application of FEA, I highly recommend the book, “Building Better Products with Finite Element Analysis”.
What Are The Advantages Of FEM And FEA?
1. Faster Design Development
The primary advantage of FEM and FEA is that they allow engineers to analyse complex systems quickly and accurately. This can save significant amounts of time, money, and resources in the engineering process by reducing the need for physical testing or experimentation.
2. Provides Addition Information
FEM / FEA can provide detailed information about a system that would be difficult to determine through other means.
For example, it can show the complex stress response of a component, and highlight any weaknesses or problems before manufacturing.
3. Design Accuracy
FEM and FEA are highly versatile tools that can be used to analyse almost any type of physical system.
Depending on the skill of the simulation analyst, FEA / FEM can provide accurate results for a wide range of loading conditions, so engineers can get an accurate picture of how a structure or system will behave under different scenarios.
4. Cost Effective
Finally, computerised versions of FEM and FEA make it easy for engineers to perform complex analyses with minimal effort and cost.
Thousands of dollars can be saved in the product design lifecycle by using FEA /FEM, as designs can be tested in a virtual environment before making costly physical prototypes.
What Are The Different Types Of FEM?
FEM can be used for a wide variety of complex engineering problems, from structural problems to thermodynamic problems.
Here is a list of some of the different types of FEM
1. Linear Elastic Analysis
2. Nonlinear Analysis
3. Stability and Buckling Analysis
4. Contact Stress and Friction Analysis
5. Thermal Stress and Heat Transfer Analysis
6. Fluid Dynamics Analysis
7. Wave Propagation, Vibration, Acoustics, Sound Radiation & Absorption Simulation
8. Non-Linear Material Behaviour Simulation
9. Structural Optimization
10 Dynamic System Modelling
Final Thoughts
In conclusion, FEM and FEA are important analytical tools that can be used to analyse a variety of physical systems quickly and accurately. They provide detailed information about the behaviour of a system under different loading conditions and have many advantages over other methods of analysis.
By using the different types of FEM to analyse complex physical systems in a virtual environment, engineers can get an accurate picture of how their designs will behave under various loading conditions before committing resources to expensive prototyping or testing.
This makes it possible for product designers to optimise their designs with minimal effort and cost while ensuring maximum accuracy.
With these advantages in mind, it is clear why so many companies have adopted this technology as part of their engineering process. When applied correctly, FEM can solve complex engineering problems while saving money in the long term.